In construction and civil engineering, the phrase ‘in situ construction’ is commonly used to describe a particular method of building and repairing construction elements.
There are a variety of different ways that in situ construction is used, and it can refer to different elements of the construction process. Using the in situ technique can have particular benefits when employed, but there are times when it is not suitable.
In this building wiki, we explore what ‘in situ’ means in construction, why it is used in projects, and what the difference is with in situ construction and other building techniques.
What is the meaning of in situ construction?
In construction, the term ‘in situ’ refers to building works that take ‘in place’ or ‘on position’ at a construction site. This is opposed to work that takes place in an off-site location, like a factory or a workshop. The most common building element that is built in situ is concrete, although the term is often referred to in soil testing.
In situ construction entails not only the preparation, assembly and finishing of the structure or component, but also testing and inspection. The continuing maintenance of the element in question is also referred to as in situ.
Where prefabricated elements need time and effort to assemble and transport structures, in situ elements like concrete are set and poured on site. As such, in situ construction is frequently more affordable and practical than other methods.
Additionally, because the work can be completed on site, it enables greater customisation and makes it simpler to modify the design to meet the unique needs and specifications of the project.
What are the benefits of in situ construction?
In situ construction is used commonly in the building world due not only to its necessity but also its benefits. One of these benefits is cost, as it is often cheaper to build something in situ or repair it rather than to take down the entire component and transport it to an off-site location. For structures that are hard to move, costs of the latter can become dear.
It is also convenient, as it does not need as much time or manpower to transport goods from one area to another. This is particularly true with hard-to-manoeuvre objects.
Additionally, because in situ work can be completed on site, it enables greater customisation and makes it simpler to modify the design to meet the unique needs and specifications of the project.
And, in situ construction can often result in a more durable and higher quality finish, as workers can apply more detail and build according to the environment to which the building stands.
How does in situ construction work?
There are a number of steps in the process of in situ construction. Typically, these are:
- Preparatory Works – preparing the site, which may involve excavation, laying foundations or grading.
- Assembly – the component in question is assembled in situ, or ‘in position’. The type of technique used here depends on the requirements of the project.
- Finishing – Materials, such as drywall, paint or tiles, are used to enhance the aesthetics and functionality of the element.
- Testing and inspection – The project is tested and inspected to make sure it is safe, and it adheres to all existing building codes and regulations.
- Maintenance – following the last touches, ongoing maintenance is performed to ensure the component acts in the way it should. Upgrades may be needed as time goes on.
However, every construction project is different, which means the timescales and steps taken to achieve the end goal differ. Part of the attraction of in situ construction is its flexibility, which allows these different steps to be taken according to the building’s properties.
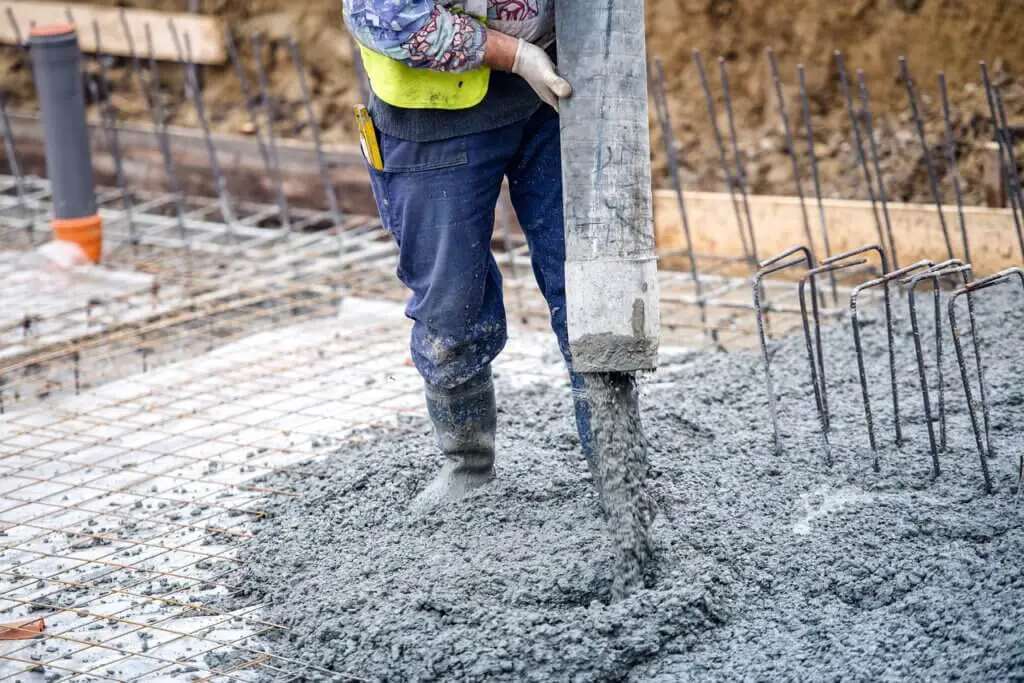
What is the difference between in situ and precast concrete?
The difference between concrete structures and precast concrete is that while in situ concrete is poured and set at the site of construction, precast concrete is set off site and transported ready-made to the location.
Instead of having the concrete built in a factory and then transported to the construction site, in situ concrete means pouring and setting the concrete on the spot. A versatile and economical method, this enables the development of components and structures that are specifically tailored to the environment and application for which they are intended.
Precast concrete has a number of benefits, including the ability to easily regulate the final product’s quality and the capacity to manufacture large numbers of standardised components. It also gives builders the capacity to speed up construction by allowing work to be done simultaneously on various project components.
The decision on whether in situ or precast concrete will be used is ultimately based on the project’s unique needs and requirements, including the structure’s size, shape, and purpose. Also taken into account are the availability of materials and labour, as well as the project’s budget and schedule constraints.
Where is in situ construction used?
In situ construction can be used in a variety of applications on a construction site. Some of the most common structural components, such as building foundations, walls, floors, and roofs, can be built in situ.
Additionally, this construction method is utilised to fix flaws or damage in already-built structures. For example, these include buildings which have developed cracks and rust, or have obtained water damage.
That’s it for our guide to the meaning of in situ construction! There’s no doubt that it’s a construction technique that saves builders time and effort, and its versatility is its strong suit.
For more news, guides and discussions from the world of urban construction and architecture, explore more of our articles here.
Or, for similar definitions and full meanings of terms similar to in situ construction, take a look at more of our wikis. They include a guide to what a ribbed vault means in architecture.
Last Updated on 10 January 2023 by Michael