Prefabricated construction, often referred to as prefab construction, is becoming more and more popular in the building industry as a go-to method of construction. It involves the use of pre-manufactured elements that are built in a factory setting, before being transported to a construction site for assembly.
Due to the nature of prefabricated construction, there are many potential advantages for building planners. It can be a cost-effective and time-efficient way of constructing buildings, hence its growing popularity.
However, it’s not always possible to build in the prefabricated manner.
In this guide, we look into what prefabricated construction means, why it is used, and its advantages and disadvantages. We’ll also explore which materials are typically employed with this construction method, and run through some well-known examples of prefabricated structures.
So, whether you’re a budding builder, architect enthusiast or merely interested in how the buildings around us come to life, enjoy our wiki on prefabricated construction.
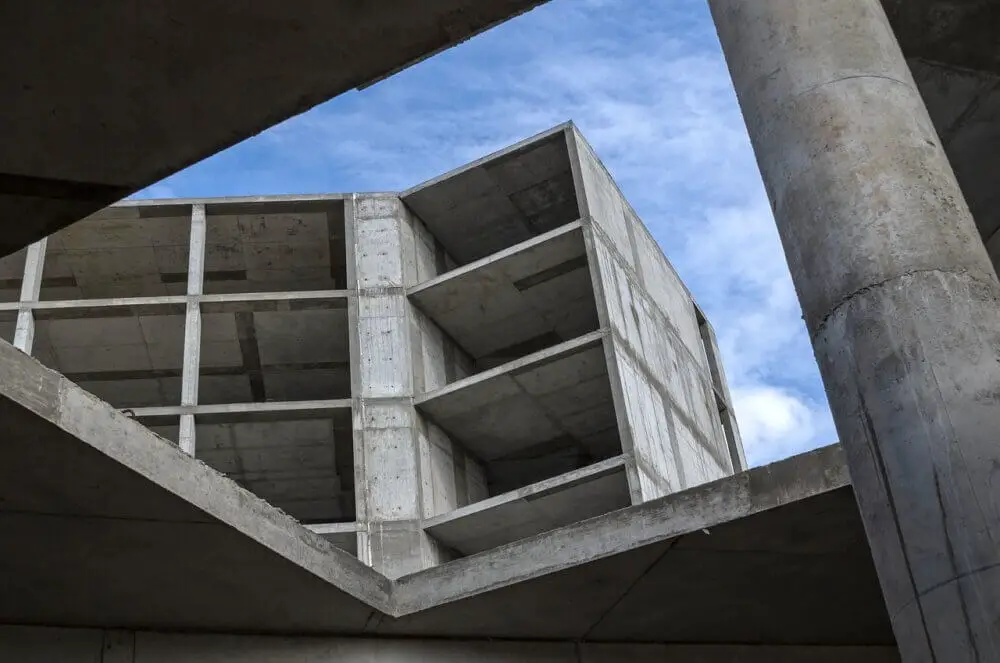
What is prefabricated construction?
In short, prefabricated construction is a building method of assembling construction elements at an off-site location, such as a factory or warehouse. These pre-manufactured components are then taken to the final location, where they form part of a wider project. Prefabricated construction has become popular in recent years as a quicker alternative to in situ construction.
Prefabricated construction can be applied to a wide variety of different building types. For instance, they can form modular homes, steel structures and precast concrete, and there are many more examples.
In one form or another, prefabricated construction has been around since the 17th Century, in places like North Africa and the Mediterranean, although the first pre-cast apartment block was not completed until 1906 in Liverpool.
The first examples of prefabricated elements being used in the modern era was after the Second World War, when there were housing shortages due to bomb damage. With little money available for re-construction, cheaper and quicker alternatives to in-situ construction were needed. Hence, prefabricated construction was born.
However, it wasn’t all plain sailing. There were a number of high-profile incidents with prefabricated elements, such as the Ronan Point apartment collapse, in the mid 20th Century, that damaged its reputation. In these developments, there were also issues with condensation and leaky connections between the prefabricated parts.
However, construction technology has improved, and prefabricated construction now is not only much safer, but easier to hide visually as well. This is because joints and panelling can be disguised a lot better, with the help of panelling and cladding.
What are the advantages of prefabricated construction?
There are some key advantages to prefabricated construction that make it a go-to method for building planners worldwide, as preferred to more traditional on-site building methods.
One of its biggest advantages is quicker construction time, as prefabricated elements can be manufactured away from a site in a controlled environment. This means less time needs to be spent on the site itself, where external factors like weather cause delays.
Other benefits to prefabrication include the ability to precisely cut and measure components, which reduces waste and boosts productivity. Additionally, the ability to build and test prefabricated parts off-site before bringing them to the job site and putting them together leads to high quality control.
And, prefabrication, in contrast to conventional construction methods, can reduce building expenses by cutting labour and material costs, while developing buildings that are more environmentally friendly and energy-efficient.
What are the disadvantages of prefabricated construction?
As well as the obvious advantages, there are some inherent disadvantages to prefabricated construction.
One of the main disadvantages is its relative inflexibility in terms of design. The capacity to adapt a building’s design is restricted, as all the parts are pre-manufactured and cannot be changed.
Meanwhile, logistically, prefabricated structures must be carried to the construction site, which can be expensive and logistically difficult. There are also often restrictions on the kind of materials that can be employed.
Other disadvantages may include limited accessibility, since prefabricated buildings might not be accessible everywhere, and the potential for zoning and permits issues. In some cases, prefabricated buildings may not adhere to zoning rules and regulations or local building codes.
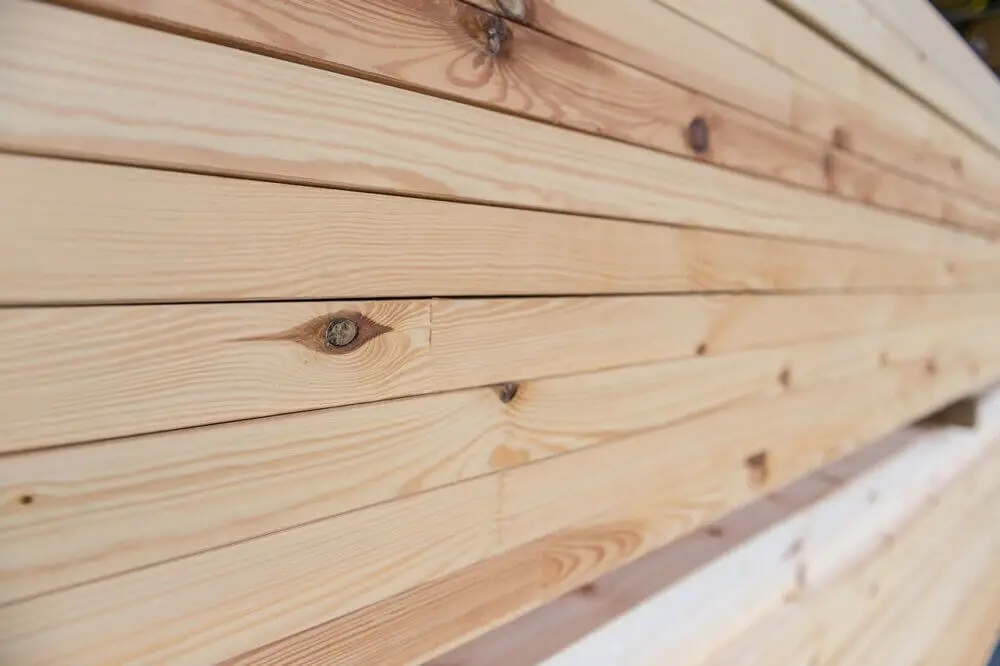
How are prefabricated buildings constructed?
There are a variety of different ways that prefabricated constructions can be built. Which one is used depends on the materials employed and the type of building that is being built.
One of the most common ways that prefabricated buildings are constructed is modular construction. This method involves building elements of a construction at a controlled factory setting, before transporting and assembling them together at the final location.
In a similar vein, panelized construction involves manufacturing component panels, typically built of wood or steel, that comprise walls, floors, and roof portions. These are intended to be rapidly put together to make the finished structure.
Meanwhile, prefabricated steel and pre-cast concrete construction employs factory-manufactured elements to erect a building’s framework. As with other prefabricated methods, the steel frame or concrete elements are then delivered to the construction site, where in this case they are used in the foundation.
Finally, hybrid construction may be used as a prefabrication technique. This is a combination of both conventional site-built construction methods and prefabrication.
What materials are used in prefabricated construction?
There are a number of different materials that are used in prefabricated construction, and how these are used depend on which building element they are being used for. Some of the most common materials include wood, as a natural insulator, and concrete and steel, due to their naturally high levels of durability.
Plastic or glass is also commonly used, typically as part of cladding or panelling. The former, especially, is lightweight and can withstand large amounts of pressure without breaking.
Meanwhile, prefabricated insulated panels may be used in a building’s envelope, in order to make a building more sustainable. These panels are usually made of materials such as polystyrene and polyurethane.
What are some examples of prefabricated building elements?
There are examples of prefabricated elements in buildings of many different types. Some of the most common include:
- Walls: walls that are created at a controlled facility before being shipped to the construction site. A range of materials, including wood, steel, concrete, and insulated panels, can be used to build them.
- Flooring: flooring components that are created in a factory and then delivered to the on-site location. They can have insulation and electrical conduit, and are often built of concrete, steel, or wood.
- Façade: cladding made of precast concrete, sandwich panels, or other materials that are manufactured in a factory before being delivered to the place of construction.
- Roof trusses: roof trusses that are pre-manufactured in a controlled environment. They can be made from wood or steel and used to support a variety of roofing materials.
- Stairs: pre-constructed stair units, made from wood, steel or concrete, that can be used for both indoor and outdoor applications.
- Bathroom and kitchen units: bathroom and kitchen units, such as kitchen sinks, toilets and plumbing units. A variety of materials can be used in these constructions.
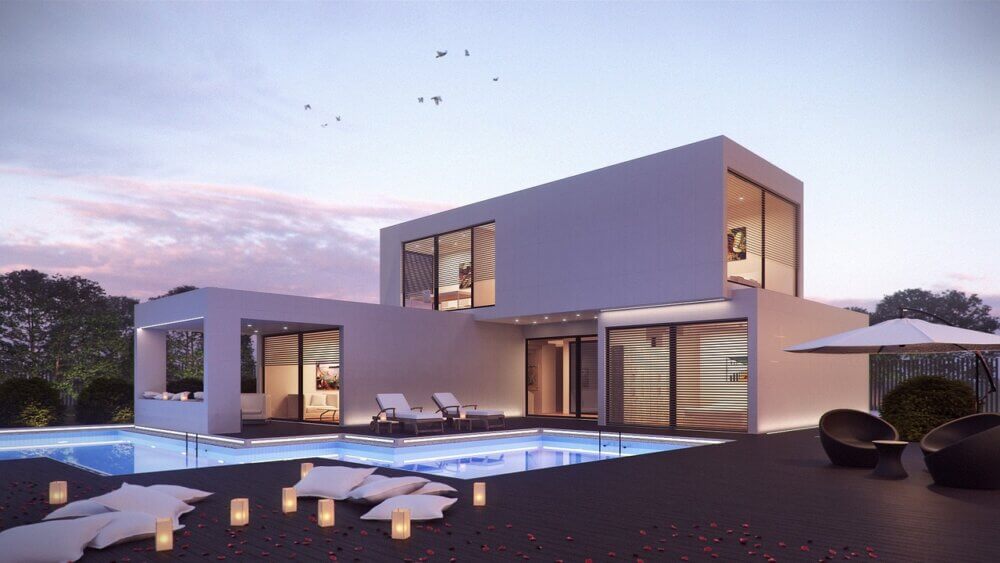
What is the difference between prefabricated construction and in-situ construction?
Put simply, the difference between pre-fabricated construction and in-situ construction is that they represent two different ways of constructing a building.
On one hand, prefabricated construction entails the assembling of structural elements in an off-site, controlled environment, before they are moved to the site itself. In-situ construction, on the other, is a more traditional building style that involves completing all building work at the site itself.
Where prefabricated construction relies heavily on machinery to guide its building work within a controlled setting, in-situ construction tends to feature manual labour for logistical and practical reasons.
That’s it for our building wiki on prefabricated construction. There are definite advantages to this construction method – it’s quicker, cheaper and arguably more precise than in-situ construction.
However, it is not always suitable for employment, due to its relative design inflexibility and logistical drawbacks. So, it won’t be the only construction methods used in building projects any time soon!
For more news, compilations and discussions from the world of urban construction and architecture, explore our selection of articles.
Or, for similar guides to definitions and meanings of terms within the building profession, take a look through our range of building wikis, including a guide to what is a ha-ha.
Last Updated on 29 January 2023 by Michael